Seeing is believing.
Book a demonstration of our unique Integra® cylinder.
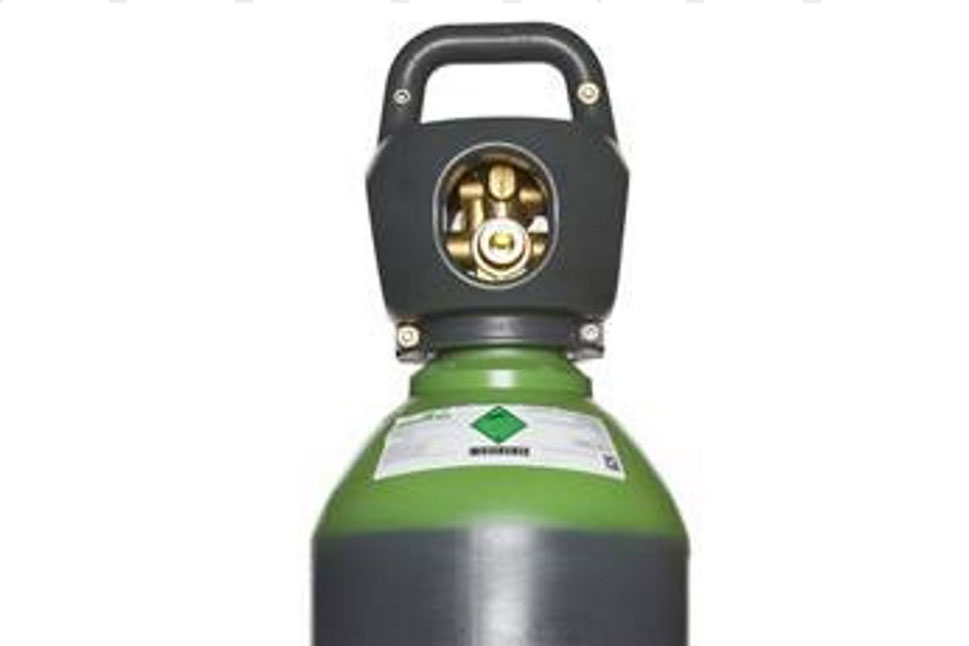
Minimise risks associated with cylinder handling
- Built-in regulators on the welding gas cylinder reduce exposure to pressure hazards.
- Lower centre of gravity reduces the risk of cylinder toppling.
- Smaller, shorter cylinder dimensions mean easier to manoeuvre and require less storage space – ideal for a busy workspace.
- Range of portable cylinders within manual handling guidelines to reduce risk of MSD injuries.
- Oxy-acetylene cutting cylinders can only be used if Integra® flashback arrestors are attached.
Time saving features mean more time welding
- The click-on Integra® Flow Optimiser (IFO) connection reduces cylinder changeover time by 30%* (*compared to conventional 200 bar cylinders)
- No bottle keys or tools are required to change over the cylinder.
- Ergonomic features ensure easier movement: handle (welding gas cylinder) and rolling knob (o-acetylene cylinders)
Download Integra® cylinder brochure
Our innovation for safer welding, cutting and brazing
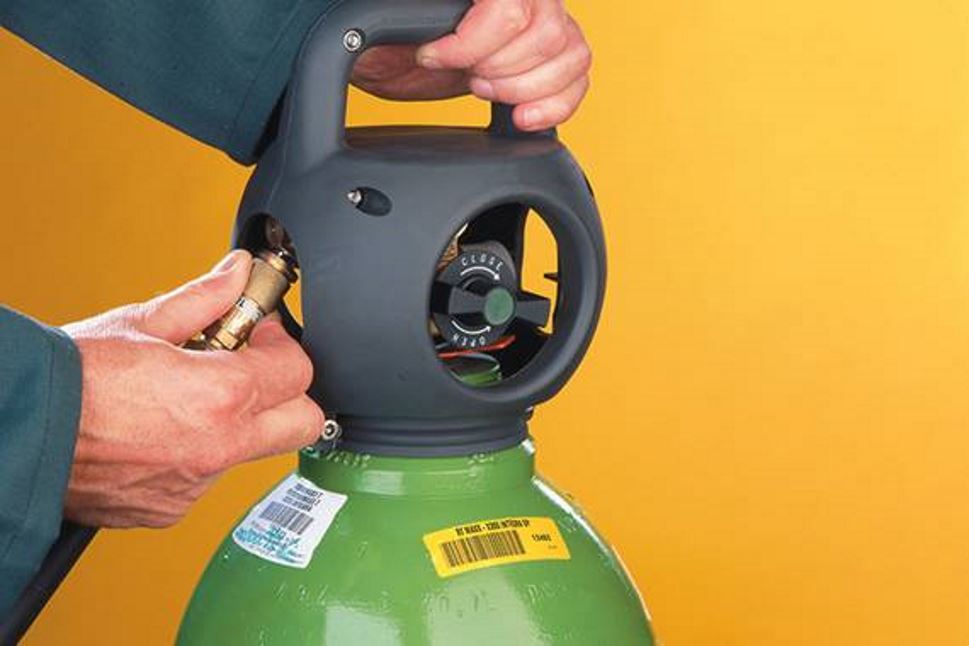
Integra® Flow Optimiser (IFO)
- Integra® cylinder connects easily via quick-connecting Integra® Flow Optimiser (IFO).
- A range of IFOs available with pre-set gas flow rates from 8-20 l/min ensuring constant control so you only use the gas you need for optimal weld quality.
- Built-in regulator reduces equipment costs
- Smaller, shorter cylinder requires less storage space, ideal for a busy workspace
- Cylinder often lasts longer than conventional cylinders* (*200 bar) meaning less time spent on cylinder changeovers
Integra® Cylinder Range
APPLICATION | GAS | PR CODE | SIZE | VOLUME | WEIGHT | MIX |
---|---|---|---|---|---|---|
MIG/TIG stainless steel, aluminium; TIG carbon steel | Argon | 169034 | 10 litre | 3.03 m3 | 17.01 kg | Ar |
MIG/TIG stainless steel, aluminium; TIG carbon steel | Argon | 14292 | 30 litre | 9.08 m3 | 64.38 kg | Ar |
MAG all carbon steel | Ferromaxx® Plus | 160263 | 30 litre | 8.73m3 | 61.54 kg | ArHeC20/12 |
MAG carbon steel >10mm thick | Ferromaxx® 15 | 403546 | 30 litre | 9.59 m3 | 65.64 kg | ArCO15/2.5 |
MAG carbon steel <10mm thick | Ferromaxx® 7 | 14413 | 30 litre | 9.21 m3 | 65.64 kg | ArCO7/2.5 |
MAG all stainless steel | Inomaxx® Plus | 160261 | 30 litre | 8.09 m3 | 64.49 kg | M12ArHeC35/2 |
MAG thin stainless steel | Inomaxx® 2 | 160258 | 30 litre | 9.00 m3 | 64.49 kg | M12ArC2 |
TIG stainless steel | Inomaxx® TIG | 500775 | 30 litre | 8.87 m3 | 65.49 kg | R1ArH2 |
MIG/TIG aluminium & alloys | Alumaxx® Plus | 160259 | 30 litre | 8.14 m3 | 59.29 kg | 13ArHe30 |
Fuel cutting | Oxygen | 123532 | 30 litre | 9.15 m3 | 61.64 kg | O2 |
Fuel cutting | Acetylene | 123805 | 30 litre | 6 kg | 60.00 kg | C2H2 |
FAQs
Our Integra® cylinder features integrated flow optimisers - this great precision engineered device ensures the optimum pre-set flow for your welding process.
"Is the cylinder supplied with an IFO (Integra® Flow Optimiser)?"
No. There are 6 different IFOs with flow rates ranging from 8-20 l/min. You need to order the required IFO/s for your process when you order a cylinder for the first time.
"How do cylinders last so long is there is less gas?"
On average there is 10% less m3 gas in the Integra® cylinder compared to conventional 200 bar cylinders. However as the IFO ensures a constant gas flow rate, excessive gas consumption and waste is eliminated meaning the cylinders often last as long.
"How do I know how much gas is left in the cylinder?"
The Integra® cylinder has a contents gauge which always shows how much gas is left even when the cylinder is not in use.
Benefits of our Maxx® Gases
Maxx® gases have a positive impact on various aspects of the welding operation leading to an overall lower cost per metre welded:
- Lower reject rates – greater weld penetration, minimal defects
- Visual improvements – smoother, cleaner, brighter welds
- Higher productivity – up to 35% increase in manual weld travel speeds and less post-weld cleaning
- Lower wire consumption – flatter welds and minimal spatter generation
- Reduced power consumption
Ready to order?
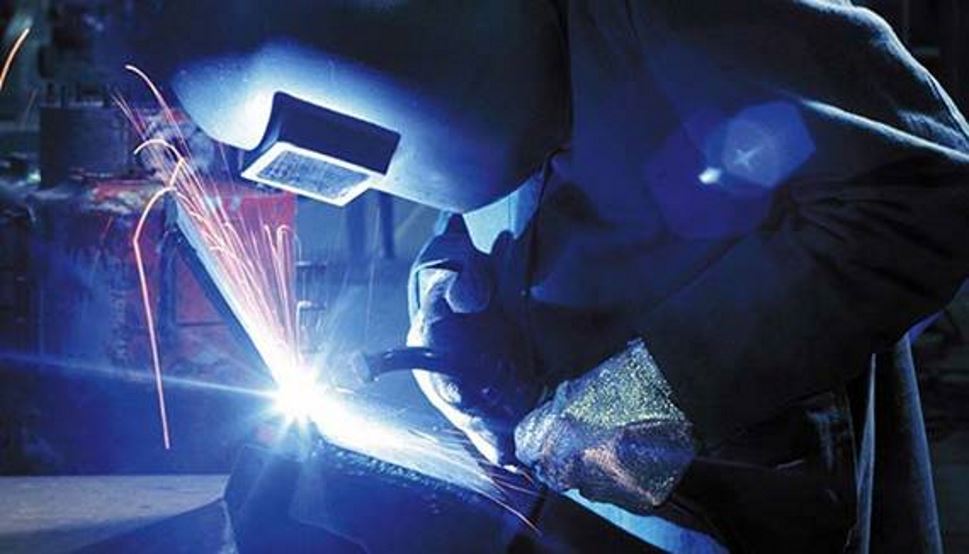
Are you sure you’re really controlling your welding gas flow rate?
Why is it important to control the shielding gas flow rate?
A uniform flow of gas is needed to shield the molten metal by blanketing it properly to avoid atmospheric contamination.